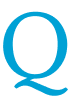
Warning letters, 483s, Recalls, Import Alerts, Audit observations
WHO has published a comprehensive and easy to understand guideline for control of nitrosamines in pharmaceutical products. The TRS 1060 – Annex 2: WHO good practice considerations for the prevention and control of nitrosamines in pharmaceutical products is applicable for manufacturers and packers of APIs, excipients, processing aids, and finished pharmaceutical products (FPPs). The guideline makes it clear that Manufacturers must perform risk assessments and ensure nitrosamine impurities do not exceed acceptable limits and Importers and distributors must ensure they receive risk assessment documentation from manufacturers.
The guideline provides a thorough framework for conducting risk assessments covering premises, equipment, materials, route of synthesis, production process, and interaction between chemicals, excipients, solvents, APIs, and packaging components, as well as the dosage form and the intended use of the product.
Potential Sources
The guideline elaborates the potential causes for nitrosamine formation and contamination – amines reacting with nitrosating agents, different sources of amines and nitrosating agents and nitrosamines such as excipients, processing aids, process water, printed packing materials, recovered solvents and processes sharing common equipment. Apart from these the guideline highlights few specific sources of contamination such as recycled catalysts, recycled reagents, equipment through passivation of stainless steel (SS) surfaces using nitric acid, inlet air in fluidized bed dryers (FBDs) carrying nitrogen dioxide (NOâ‚‚) as potential sources for nitrosating agents and nitrosamine contamination. Manufacturers should consider all these potential sources in their risk assessment. The WHO guideline also gives a nice definition of nitrosating agent as a substance that has the potential to transfer a nitrosyl group (-NO) to a primary, secondary, or tertiary amine, leading to the formation of the corresponding nitrosamine and elaborates these nitrosating agents.
Controls for API Manufacturers
The guideline asks API manufacturers to carefully design route of synthesis, optimize processes and reaction conditions (such as pH, temperature and reaction time) to minimise formation of nitrosamines and facilitate the purge of nitrosamine impurities. The guideline suggests to avoid reaction conditions that may produce nitrosamines, exclude those with secondary amines, replace nitrites with other quenching agents for azide decomposition processes. Recovered solvents to be used only in same step or previous steps within the same process, ensuring proper purification. API manufacturers should perform comprehensive risk assessment, audit supply chains, verify use of any recovered materials in the processes of raw materials and reagents, verify and control nitrites and nitrosamines if required in process water. Where a risk is identified API batches shall be tested for nitrosamines and if risk is high with nitrosamines detected above 10% acceptable intake (AI) limit) controls measures should be implemented.
Controls for FPP Manufacturers
FPP manufacturers should conduct risk assessment to determine potential sources of nitrosamines covering evaluation of supply chain, excipients, API processing, utilities, storage, repackaging, degradation during storage, generation during shelf life. Nitrosating impurities such as nitrites are possible in a range of commonly used excipients with wide batch to batch variation. FPP manufacturers shall ensure control measures with due consideration of quantity of excipients used in the formulation, variability in nitrite content across excipient batches, and processes with higher risk of nitrosamine formation such as granulation and drying in solid dosage forms. Manufacturers of excipient shall perform the risk assessment for nitrosamine formation in their manufacturing process and take control measures. Printed packaging materials may also be a source of contamination due to nitrocellulose and amines in printing ink. FPP manufacturers supplier qualification programmes should cover the verification of controls over the possibility of amines, nitrosating agents and nitrosamines from excipients and packaging material and implement control measures. When risk for nitrosamines is identified, confirmatory testing should be conducted using validated analytical procedures. The guideline asks FPP manufacturers to implement mitigation measures if the nitrosamines are more than 10% of the Acceptable Intake (AI) limits thus making it clear that specification control of nitrosamines to defined acceptable intake (AI) limits alone is not enough
Comprehensive framework and questionnaire for risk assessment
The WHO guideline also provide a detailed framework for conducting root cause analysis to identify potential nitrosamine risks in pharmaceutical manufacturing and outlines a comprehensive set of questions for root cause analysis to identify potential nitrosamine risk. Manufacturers must perform comprehensive risk assessment covering all pertinent risk elements and implement effective control measures to prevent and control of nitrosamines in pharmaceutical products The risks should be also reassessed periodically.
Leave a Comment
You must be logged in to post a comment.