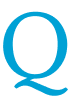
Warning letters, 483s, Recalls, Import Alerts, Audit observations
The FDA has issued new guidance on “Considerations for Complying With 21 CFR 211.110.” According to 21 CFR 211.110, manufacturers are required to establish and follow written procedures that describe the in-process controls, tests, or examinations to be conducted on appropriate samples of in-process materials for each batch to assure batch uniformity and integrity of drug products. Such control procedures could include, but are not limited to, weight variation, disintegration time, blend uniformity, content uniformity, dissolution time, clarity of solution, pH of solutions, and bioburden testing. The quality unit is responsible for ensuring in-process materials are tested for identity, strength, quality, and purity as appropriate and for approving or rejecting in-process materials during the production process. Not complying with the requirements of 21 CFR 211.110 and cGMPs can lead to the FDA considering a drug to be adulterated under section 501(a)(2)(B) of the Federal Food, Drug, and Cosmetic Act.
The FDA’s guidance expands on the expectations outlined in 21 CFR 211.110. Manufacturers should define the significant phases in their manufacturing processes and justify when and where appropriate tests or examinations should occur. These phases can vary depending on the methods used and the nature of the individual products. Manufacturers should identify critical quality attributes (CQAs) and in-process material attributes that need to be monitored and controlled to ensure drug product quality. The guidance allows flexibility in how in-process testing is conducted. In-process testing does not always require the physical removal of samples for laboratory testing. Innovative technologies such as in-line, at-line, or on-line measurements can be used to monitor critical attributes in real-time. The guidance emphasizes that in-process testing should be conducted based on a scientifically sound and appropriate sampling and testing strategy. This can include time-based sampling plans and surrogate measurements (e.g., time-based measurement of the change in dryer outlet temperature as a surrogate for moisture content) to ensure drug product quality. The guidance also clarifies that process monitoring and control decisions that result in minor equipment and process adjustments do not typically need additional quality unit approval if all of the following conditions are met: (1) the adjustments are within the pre-established and scientifically justified limits; (2) these limits have been approved by the quality unit in the master production and control record and the control strategy; and (3) the production data is reviewed by the quality unit before approval or rejection of a batch.
The guidance emphasizes that compliance with 21 CFR 211.110 is critical, even when using advanced manufacturing techniques. The guidance reiterates that manufacturers must comply with the requirements of 21 CFR 211.110 to ensure batch uniformity and drug product integrity, regardless of the manufacturing approach used. However, in advanced manufacturing like 3D printing or continuous manufacturing, some significant phases may be combined or approached differently compared to traditional batch processing. For example, in batch manufacturing of a solid oral drug product, blend uniformity should be assessed before in-process materials are released to the compression stage. In continuous manufacturing, sampling and testing could be at the tablet press feed frame or after compression. The FDA guidance also cautions against relying solely on process models for in-process control strategies in advanced manufacturing. For example, a process model can predict the uniformity of a powder blend by analyzing data from sensors placed throughout the manufacturing line, detecting deviations, and triggering adjustments to the process parameters to maintain product quality. The guidance emphasizes that while process models can be powerful tools, they have limitations, especially when unplanned disturbances occur during the manufacturing process. These disturbances can invalidate the underlying assumptions of the process models, making them insufficient to ensure product quality on their own. To address this, the guidance advises a combination of in-process controls based on process models and in-process material testing. The combination of process models and in-process material testing provides a more robust and reliable control strategy, capable of handling unexpected variations in the manufacturing process.
The guidance assumes significance in the background of different FDA observations on inadequate in-process controls. For example, in a USFDA 483 issued to Granules India in September 2024, the FDA observed that batches were allowed to proceed to the compression stage even though in-process tests were failing at the blend stage.
In summary, the guidance emphasizes that compliance with 21 CFR 211.110 is critical. Manufacturers must define significant phases, identify critical attributes to monitor, and ensure that appropriate criteria are defined and monitored to assure batch uniformity and integrity of drug products.
Leave a Comment
You must be logged in to post a comment.