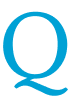
Warning letters, 483s, Recalls, Import Alerts, Audit observations
Zydus Jarod facility (FEI 3013712903) is classified OAI by USFDA in July 2024. The USFDA inspection at the facility by USFDA investigators Justin A Boyd and Anastasia M Shields in April 2024 had observed critical deviations. The deficiencies include failure to exhaustively evaluate impact of cross contaminations due to cleaning lapses and recall all potentially impacted batches. The Firm also allowed products with potential glass particle contamination to stay in the market. Critical data integrity concerns were flagged with samples from same point used to generate multiple results to show results of samples from all sampling points. Samples were routinely collected by fixed term employees not trained for the activity, but qualified employees signed off for sampling. Deficiencies were also observed in the software system for microbiology documentation of sampling and testing. Analysts were able to override the data captured by barcode scanners with manual entries without audit trail. Â
Multiple deficiencies were observed in aseptic area and aseptic practices. Unidirectional flow was not demonstrated during operator interventions. Operators were also seen to use non sterile tools for contacting sterile components, and operator interventions disturbed laminar airflow posing risk to sterility of the drug products. Even equipment were observed with scratches and rough surfaces. It was also observed that the operators involved in visual inspection of vials were not qualified adequately for identifying glass particles at the range observed in batches.
Deficiencies were observed in Process validation studies. Investigations on customer complaints on not able to withdraw full contents of vial for administration did not evaluate process validation studies whether vials were stoppered completely. No destructive or non-destructive tests were performed in any of the products. Process validations were also found to be deficient in that it failed to verify intra and inter batch variability for parameters like assay, impurities, pH etc with appropriate acceptance criteria.
Other deficiencies observed include inadequate chromatographic integration practices with different processing methods being used for chromatograms within same sequence without meaningful documentation, Handling of Errors and alarms in the Non-viable particle monitoring. Inadequacies were also observed in cleaning validation studies with incorrectly identified hardest to clean API and failure to assess cleanability on full range of surfaces.
Learnings
Comprehensive Investigations
Inadequate investigations and impact assessment is an often-cited observation in FDA inspections. When incidents of contamination are observed its imperative that an exhaustive assessment of extent of contamination is performed. When unknown peaks are observed above limits in some batches, other batches and products also need to be investigated for similar potential contamination. Contamination in other batches might have gone unnoticed because the peaks were below the reporting threshold. But cross contamination do not have any limits applicable! Limits are applicable for related impurities and unidentified impurities generated / internal to the drug product. When residues were left behind due to deficient cleaning causing contamination in the next product, such residues and their degradants can be a cause of concern within batches of same product as well where batch to batch cleaning performed will be less exhaustive. This also need to be evaluated, including the capability of the analytical methods to detect such residues and degradant impurities.
In incidences of glass particulates contamination in products due to sample – vial interaction or  incompatibility of product with vial, not only the batches where the issue is noticed, other batches and products with same /similar vial are potentially at risk. When vials are not compatible with one product leading to generation of glass particulates, other products with similar matrix also could be impacted. This need to be assessed and there should be strong scientific justification if it is not a potential risk. In failure investigations, contamination issues etc when the initially identified root cause was not the actual cause or was not the only cause, the initial impact assessment also become incomplete. Batches released based on such impact assessment need to be reevaluated for contamination.
Quality oversight
The above issues also highlight the issue thoroughness of investigation and Quality unit oversight. Investigation of issues like repeated failures of injection vials for glass particulates should be comprehensive considering all possibilities including vial compatibility. Inadequate investigation, incorrect root cause, incorrect CAPA and recurrence of issue increases the magnitude of impact several fold. This also point to the need of wholesome product development where compatibility issues are evaluated. When changes like new materials, new sources for material are introduced, one should assess whether all the evaluations and studies performed during product development support the change or additional evaluations are necessary. There need to be a robust change control system to ensure the same.
Data Integrity, Quality Culture
Generating results for multiple samples with a few samples, signing off documents for activity not performed are all clear cases of data integrity. This highlights the importance of Quality oversight and control over the operating personnel. This also flags issues in the GMP orientation and Quality culture. Addressing these issues requires a comprehensive approach, including stern action against misconduct, initiatives for improving Quality culture and management oversight, frequent internal audits, surprise inspections by third party resources, thorough training and development of personnel including behavioural training and management reviews with involvement of executive management. Computer systems used for all quality operations should be in adequate control complying to the electronic data controls (21CFR Part 11, EUGMP Annex 11). Computerised tools like bar code scanners which directly capture sample data, location, date and time of sample etc are useful tools. But if they are not controlled to prevent overriding electronic data with manual entries, data deletion, entries by unauthorised persons, with systems lacking date and time stamp and audit trail of changes, integrity of the electronic data cannot be assured.
Aseptic Operations and Prevention of Microbial Contamination
Unidirectional airflow under dynamic conditions and during operator interventions are critical controls to ensure sterility assurance in aseptic areas. Airflow visualisation studies should be able to demonstrate the unidirectional flow. Maintaining integrity and sterility of aseptic processing environments is critical to prevent microbial contamination. Listing out all possible operator interventions, evaluating the interventions for any disturbance of the laminar flow by smoke studies and correcting where required, detailing acceptable operators interventions and monitoring the same during media fill studies, defining approved interventions for ascetic operations, monitoring the routine batches for operator interventions and mark any deviations, risk assessment of the deviations including batch impact, smoke studies where required to evaluate the non-routine / unapproved interventions, validating the new interventions in further media fill studies and updating the approved interventions is a continuous cycle to be practiced for robust control of aseptic operations. Periodic operator training to reinforce proper aseptic techniques and awareness of approved interventions is essential to ensure operators understand the importance of their role in maintaining sterility and the impact of their actions. scratches and rough surfaces on equipment components and accessories can act as reservoirs for contaminants and microbial build up. Implement robust maintenance programs to regularly check equipment components and take corrective actions. Afterall why should it take an FDA inspector to identify such gaps.
Qualification of Personnel for Visual Inspection
The presence of particulates in injectable products can pose serious risks and adverse events including inflammation, embolism and life-threatening blood clot events. The regulatory requirements clearly define that inspection process for particulate matter should be designed and qualified. For qualification of personnel libraries of defective units from samples collected throughout product life cycle should be developed to cover the actual particle size range of contaminants observed in visual inspection. This should contain examples from the lower limits of visual detection determined in threshold studies. (USFDA Guidance: Inspection of Injectable Products for Visible Particulates).
Process Validations, Container Closure Integrity Testing, Intra-Inter batch variability
Container closure Integrity testing is essential to assure its suitability for protection against microbial contamination, reactive gases like oxygen, ingress of air, moisture. EUGMP Annexure 1 require that samples should be taken and checked for integrity using validated methods with a scientifically justified sampling plan. Visual inspection alone is not considered acceptable as critical defects compromising container closure integrity like breakage, seal defects, over crimping, stopper distortion, deformation could be missed. The USFDA guidance on Submission Documentation for Sterilization Process Validation also require container closure integrity testing to demonstrate integrity of the microbial barrier. Demonstrate container closure system integrity as part of process validation with a suitable and scientifically justified sampling plan and test methods. (For e.g.  Zero Acceptance Number sampling plan (e.g. ISO 2859-1), Reference: Sample Sizing Approaches for Container Closure Integrity (CCI) Testing; American Pharmaceutical Review).
FDA audits have pointed out in many 483s and Warning letters failure to evaluate intra and inter batch variability of drug products. The FDA guidance on Process Validation categorically states the need to collect adequate samples during different unit operations and evaluate CQAs (like assay, impurities etc) to provide sufficient statistical confidence of quality within a batch and between batches and define statistical metrics for intra and inter batch variability. It is not sufficient to evaluate the results against specification limits as acceptance criteria. During process validations, evaluate variability with appropriate statistical criteria giving due consideration for process development data. For e.g. %RSD (relative standard deviation) criteria like 5% for intra batch variability, 10% for intra batch variability.
Other Deficiencies – Chromatographic Integration practices, Equipment Alarm handling, Cleaning Validation
Different processing methods for different chromatograms within a sequence also raises concerns of integrity. This should be supported by meaningful justification and documentation with evidence – for e.g. sample matrix variation, misrepresentation of peaks, baseline drift, coelution of peaks.
Evaluating error messages and alarms in equipment and instruments help in identifying trends and recurring issues and take timely actions. Quality oversight should ensure the defined procedures are followed to report discrepancies like frequent errors, alarm handling in equipment.
While defining cleaning validation programmes and picking the worst case product, product with the least soluble API may not be always the hardest to clean. Factors like adherence property of the product to equipment surfaces, product matrix & excipients used in the product, composition of the product and concentration of the API in the product etc. may also have a role in cleanability. Also, careful consideration has to be given to ensure that the longest equipment train covering all type of surfaces to be considered in cleaning validation. If there are specific equipment used in only few products, it may be required to validate cleaning efficacy in such equipment through a separate protocol. When incidents like OOS in cleaning validation sample results, cross contamination etc happen, assess the cleaning validation activity performed and validity of aspects like hardest to clean product, equipment train and surfaces.
The USFDA 483 observations provide valuable lessons for the Pharma Industry. Review the systems and processes to identify similar gaps and take prompt remediation actions before they escalate into critical deficiencies noted during regulatory inspections, potentially leading to severe consequences.
Leave a Comment
You must be logged in to post a comment.