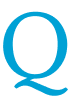
Warning letters, 483s, Recalls, Import Alerts, Audit observations
Warning letter / Centrient India / MARCS-CMS 640196/ 320-23-06/ DECEMBER 07, 2022/ Observation 2
USFDA Warning letter to Centrient India (Toansa, Punjab FEI 3004497364) in December 2022 highlight inadequate contamination control systems and practices – method for detecting beta-lactam residue in the non-beta-lactam buildings is not sensitive, validation of the test method, swab sampling and recovery studies inadequate.
Contamination of non-beta-lactam drugs with beta-lactam drugs and residues presents great risk to patient safety, can cause severe allergic responses in susceptible patients including potential anaphylaxis and death. FDA stated that no safe level of penicillin contamination has been determined to be a tolerable risk.
The Warning letter followed USFDA inspection at Centrient India site in June-July 2022. The site was inspected by USFDA investigators Joel D Hustedt, Marcellinus D Dordunoo.
Failure to ensure test procedures were appropriately validated and established procedures were followed. For example, recovery studies were not adequate to demonstrate that the method for betalactam environmental monitoring can recover beta-lactam residue by swab sampling. Established procedure for swab collection was not followed.
Firm response indicates there is no impact to product quality. However, response is inadequate because justification is based on testing performed by a method used to detect beta-lactams in the buildings where non-beta-lactam drugs are manufactured that was not appropriately validated and was not followed. Additionally, firms method for detecting penicillin in environmental monitoring of beta-lactams in the non-beta-lactam buildings is not sufficiently sensitive to detect very low levels of contamination. For additional information, see FDA’s published analytical method that has a limit of detection (LOD) of 0.2 ppb at https://pubmed.ncbi.nlm.nih.gov/29766324/.
Because of the extremely low threshold dose at which an allergic response could occur, beta-lactam facilities need to be complete and comprehensively separated from non-beta-lactam facilities. For additional information, see FDA’s guidance document Non-Penicillin Beta-Lactam Drugs: A CGMP Framework for Preventing Cross-Contamination.
Firm to provide:
FDA Warning letter observed:
FDA did not accept the Firms claim that there is no impact to product quality. The FDA contended that the method for detecting penicillin in non-beta-lactam buildings is not sufficiently sensitive. The Warning letter also highlighted that because of the extremely low threshold at which allergic responses can occur FDA expects beta-lactam facilities to be completely and comprehensively separate from non-beta-lactam facilities.
FDA asked Centrient to provide a comprehensive assessment of its laboratory practices, procedures, methods and analyst competencies and a detailed remediation plan. Firm should also perform a comprehensive assessment of the containment control systems to prevent beta lactam cross contamination including from air exhaust of beta-lactam manufacturing buildings and common shared areas like the cafeteria. The test method for analysis of beta-lactam contamination in environment and non-beta-lactam products should be validated and shown to achieve a Limit of Detection (LOD) equal to or better than 0.2ppb.
When an FDA inspection cites critical deficiencies, evaluation and assessment of the observations cited, their impact on batches manufactured & distributed and remediation actions should be comprehensive. It shall be performed against a protocol with defined scope and conclusions drawn should be scientifically sound. The CAPA plan shall address:
Identify gaps and take remediation measures as necessary.
Based on the assessment develop a plan for improving laboratory systems and procedures, competency of analysts, hiring experienced and competent personnel, training and coaching of the analysts.
References
Leave a Comment
You must be logged in to post a comment.