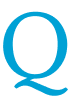
Warning letters, 483s, Recalls, Import Alerts, Audit observations
USFDA 483 issued to Dr.Reddys (DRL) API unit in Pydibhimavaram, India cites failure to validate all analytical methods, failure to maintain manufacturing processes in validated state, Investigations and root cause into OOS and failures were not scientifically sound. The 483 also observes batches were released without completing Particle size analysis. The DRL site (FEI 3002949085) was inspected by USFDA Investigators Joseph A. Piechock and Tamil Arasu in June 2024 and issued USFDA form 483 with four (4) observations.
Methods used in API testing were not Validated
On the analytical method validations, the form 483 observes, rather unusually, that the site did not validate analytical methods for identification by IR, identification by Mass spectra, tests for specific optical rotation, XRD Test, water estimation by Karl Fischer (KF) and Coulometry and XRD test. A more serious observation on analytical validation cite an incident where an unknown impurity observed during residual solvent analysis was identified, a limit was established and batches analysed and released by a GC developed method, but method was not validated. Later an Ion chromatography method was developed and validated for estimation of the impurity, but batches released earlier with the GC method were not retested by this validated method. Customer was also not intimated about the detection of the impurity and application of the limit for the impurity for more than a year. The GMP regulations (21 CFR 211.165 and 211.194.) require analytical methods to be validated and suitability verified under actual conditions of use.
Manufacturing processes indicate inadequate process control, not in a validated state
The auditors raised concern about the adequacy of process validation and control. Process validation is not holistic and indicate inadequate process control and potential for non homogeneity in the batches. In a two-year time span in, there were 17 (seventeen) OOS incidents in an API and all the batches were reprocessed. Different root causes were hypothesized and CAPAs proposed for the failures. In the reproceed batches, one OOS incident of the API was attributed to smaller API particles in the batch and another OOS was attributed to improper sampling for inprocess testing. The purpose of process validation is to establish that the process and process controls are adequate to deliver quality product consistently. If an API fails during final testing despite a passing result in an inprocess test, it could be indicating non homogeneity in the batch. When a “validated process” gives repeated OOS results, with different causes each time, it raises questions on the validated status of the process and adequacy of process controls to deliver consistent product.
Deviations not adequately reviewed; Root causes are not scientifically sound
The form 483 also observed that discrepancies and deviations are not adequately reviewed and the root cause identified for the failures often were not supported with scientific evidence. The CAPAs were inadequate to address the identified root causes to prevent recurrence. Examples are cited where root cause for a stability OOS was attributed to exposure of sample during sampling to light/air, another OOS to air bubble in potentiometer dispensing tube. An OOS of multiple lots of an API for residual solvent was attributed to cleaning of sampling area while another OOS of an API for residual solvents was attributed to inprocess sampling. In an issue of an unknown peak in residual solvents analysis of multiple batches of an API, root cause attributed to an impurity in a key starting material. A corrective action was taken to maintain a higher volume during operation. But in 4 months time the action was reversed in October 2020. Since the reversal there were 60 (sixty) incidents of unknown peak with same root cause but no corrective actions were implemented till Sep 2023. There was also an incident of a cleaning sample failing for residual solvent which was attributed to contamination of the container used for rinsing. Corrective actions including cleaning procedures in between solvent changes were implemented. A similar incident recurred in nine (9) months’ time but the investigation did not assess other cleaning records for lack of instructions. Key point to note is that the auditors are connecting the multiple OOS incidents and discrepancies in API batches, to inadequate process controls and raises questions on validated status of the process.
Batches are released without completing Particle size analysis:
The form 483 also observes API batches were released without completing Particle size analysis (a release test) by raising change control (CC).
Learnings
The form 483 observations highlight the auditor focus areas of Manufacturing process and their Control and state of Process Validation, Analytical method validations, Adequacy of Investigations into OOS, Deviations and Discrepancies. It also shows how observations in one area gets connected with concerns in another area.
Leave a Comment
You must be logged in to post a comment.