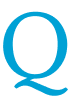
Warning letters, 483s, Recalls, Import Alerts, Audit observations
Authored by: Venkiteswaran.T.K, Subrangshu Chourdhary, Srinivas Churya
Jubilant Generics Roorkee facility was inspected in January 2024 by USFDA investigators Jeffrey P.Raimondi and Tamil Arasu. The inspection revealed lapses in failure investigations, cleaning verifications, document control, hold time studies, process validation studies and change control. Qvents reviews the observations and discusses what procedures and controls Firms should have to avoid such lapses.
Observation summary
Investigation into extraneous peaks observed in cleaning verification samples and out-of-specification (OOS) residue results was deemed inadequate. While two extraneous peaks were identified, their origin was not established, nor was a root cause determined for the OOS results. The cleaning verification report failed to acknowledge these deviations. Other additional peaks in the cleaning verification samples were yet to be identified.
What Procedures and Controls need to be in place:
Investigation into quality events must be comprehensive and thoroughly documented. All discrepancies observed during execution of study protocols should be consistently recorded in validation and verification reports to avoid noncompliance. Each discrepancy should be evaluated, efforts should be made to establish the root cause. There may still be occasions where a root cause is not identified, but these should be rare, the efforts made to establish the root cause should be demonstrated, and impact should be assessed and documented before batch release.
Observation summary
Several lapses in control of GMP documentation was observed during the inspection. Signed investigation reports created outside the EDMS and Trackwise system with no traceability or document control number were observed in locked bins for shredding. The shredder logbook was also found deficient in identifying type of document being shredded. Logbook entries for swab samples were incomplete and non-attributable. The 483 also raises issue of chain of custody of samples – samples for microbial testing were to be refrigerated if not tested on same day; but this could not be verified. It was also observed that a microbiology sample result was altered from failing to passing by the reviewer by referring to a zoomed photograph rather than the real plate. Lapses were also observed in handling obsolete recipes tablet compression machine. Control over analytical balances were inadequate and lacked audit trail features, verification of sequential print of weighing or a second person verification.
What Procedures and Controls need to be in place:
Uncontrolled Documents outside EDMS: Electronic Data Management Systems (EDMS) significantly enhance GMP and Data Integrity compliance. Yet documents may be created outside EDMS, for example annexures or other supporting information in investigations, change controls etc. Such documents should be controlled as these manual records are original and primary records. For example, EDMS system may be configured to print blank worksheets with traceable document number (incident number or investigation number) which can be used to document the investigation details just like the analytical worksheets in QC and periodically reconciled.
Chain of custody: For samples requiring special storage conditions like refrigeration, chain-of-custody of samples should be traceable. Chain of custody can be demonstrated through logbooks that record sample handling details like when, who kept the sample and removed the sample from the refrigerator. As a matter of fact, in all the logbooks all entries made should be also attributable.
Analysis and Review of Microbiology Tests: Altering / modifying analytical results or for that matter any documents, without logging a quality event, investigation, documentation and justification amount to compromise on data integrity. Ensure procedures are followed for analysis and review of test results. In microbiology tests like total bacterial count, the “Done by-Checked by” controls should include reviewing the original plates.
Electronic data control in Manufacturing equipment: For computerized systems, ensure compliance with 21 CFR Part 11 and establish manual logs where necessary. If there are limitations in manufacturing equipment with respect to archival, back up logs etc, manual records shall be maintained to log activities like creation of recipes in the equipment, changes to recipes, deletion of recipes with archiving the print outs
Audit trail, Analytical Balances: The electronic data generated by analytical balances are static data rather than dynamic. These static data are not further processed (unlike say chromatograms, spectra), hence paper print outs and verification by a second person are acceptable means of demonstrating compliance to data integrity requirements. However it doesn’t fully warrant against data manipulations. To ensure and control integrity of data companies adopt practices like specific colour prints for balances, camera recording of all weighing activities with periodic review. A more robust option is to interface balance with computer system to acquire and manage the weighing data and weighing sequence through software. The sequential weighing records can then be verified against the manual logbook to reconcile all weighing activities. (Also Refer: Peter Bakers Blog Original Records; The New Mullets @https://www.liveoakqa.com/blog-1)
Observation summary
The USFDA Form 483 also found lapses in hold time studies as they did not represent the current commercial batch size.
What Procedures and Controls need to be in place:
FDA has issued multiple 483s on hold time studies being not representative of the commercial batch size. (Torrent April 2019, Sample quantities used to establish hold time do not represent actual batch sizes; Lupin Salcette, Goa March 2017 -hold time study do not represent commercial batch size…a representative sample was collected and sample was stored in simulated containers…sample quantity requirement was regardless of the batch size and others; Alembic 2018 – batch size for establishment of hold time….. do not represent commercial batch size ). The concern in hold time studies is that if the studies are not performed with batch sizes and containers representing the commercial batch size it do not give a true picture of typical issues during intermediate storage, for example – segregation in bulk granules, impact due to humidity / hygroscopicity, oxidation etc). There is more than one approach which can be considered for conducting hold time studies, but each of them has to be appropriately justified. Lets review the typical approaches with respect to oral solid dosage forms, where intermediate hold time have higher impact.
Make an assessment of the hold time stability data of all existing products to confirm the data meet current regulatory expectations, and hold time study batch size and storage are well matching the commercial batch conditions. Many USFDA 483s on the hold time study were issued on old hold time data where hold time studies were typically performed with smaller sample sizes. One more key aspect is to ensure that during changes (like batch size changes, process changes etc), impact on intermediate hold times is also evaluated and justified.
Observation summary
When implementing changes to hardness and thickness specifications, challenge studies were performed on only one tablet strength. Moreover, the minimum number of tablets used in the 4 challenge studies – Low-Low, Low – High, High-Low and High-High – was not representative of commercial batch size. Post change effectiveness evaluation also did not evaluate all strengths.
What Procedures and Controls need to be in place:
While implementing changes to product, process and specifications, it is important to evaluate the impact on critical quality attributes like disintegration time, dissolution, hardness, uniformity etc. Establishing a design space through a DOE (Design of Experiments) study on pilot scale batches followed by a commercial batch in which CQAs are studied by a stratified sampling approach (collecting samples at 15-20 points throughout the batch) will be a preferred approach to validate the process performance. The stratified sampling and evaluation of CQAs may be performed on one strength and extrapolated to other strengths if there is strong justification with respect to similarity of formulation and manufacturing process. However effectiveness check shall be performed on all strengths and documented.
References:
Leave a Comment
You must be logged in to post a comment.