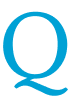
Warning letters, 483s, Recalls, Import Alerts, Audit observations
Laurus, Visakh was issued USFDA 483 with five (5) observations following USFDA inspection by investigators Joseph A. Piechocki and Rafeeq A. Habeeb in Dec 2023. The observations cite lapses in investigations of equipment damage and potential particulate contamination, OOS investigations; deficiencies in sampling to ensure representativeness of the batch, deficiencies in cleaning, verification and maintenance of equipment, lapses in documentation and control. (USFDA 483)
Qvent review the observations in a series of 3 posts. In this post Qvents review the observations of Inadequate investigation into Equipment Damages, particulate contamination, OOS investigations
Other related posts are:
Equipment Damage & Investigations
OOS Investigations / Hold time failures
Inadequate assessment of potential particulate contaminations poses risk to product quality and safety and also has regulatory consequences. When such issues are reported a comprehensive assessment shall be performed and remediation actions taken.
Review and enhance procedures for Hold time studies and OOS investigations addressing aspects to be investigated in case of failures – assessment of packing, shelf life, storage conditions for Hold time study failures; review of TAMC trends in case of TOC failures.
Leave a Comment
You must be logged in to post a comment.