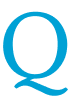
Warning letters, 483s, Recalls, Import Alerts, Audit observations
Medgel, India was issued a Warning letter by USFDA in July 2023. Deficiencies include inadequate OOS investigations and hypothesis of sample preparation error as root cause without scientific basis, inadequate investigation of deviations – several humidity excursions in manufacturing area for OTC capsules, humidity excursions in stability chambers. Warning letter cites failure of Quality Unit with Data Integrity issues including inadequate control of documents – access to documents, disposal of documents, contemporaneous documentation and review of raw data, sharing of passwords in analytical equipments, lack of procedures for review of audit trails. Warning letter also raises concern over failure of the Firm to test Diethylene Glycol (DEG) and Ethylene Glycol (EG) contamination in Glycerin, Propylene Glycol and Sorbitol used in manufacture of drug products and lapses in input component testing & controls. The Medgel site in Pithampur, MP India (FEI 3010165392) was inspected in January 2023.
Qvents review the Warning letter observations, in a series of three posts.
Observation 1
Failure to thoroughly investigate discrepancies – Out of Specifications (OOS), Deviations.
Observation 1
Failure to thoroughly investigate discrepancies – Out of Specifications (OOS), Deviations.
OOS Investigations
Repeat incidents of OOS with no clear root cause and repeatedly assigning the cause as sample preparation error (similarly laboratory error, analyst error, glassware contamination and so on), indicate issues in analysis laboratory (QC) and analytical controls.
It also shows poor investigation lacking focus to get to the root cause. The OOS incident(s) could be due to manufacturing issues as well – poor mixing, blending, granulation, storage.. but this can be missed when investigations are closed attributing laboratory errors as cause for OOS without a manufacturing investigation.
The OOS investigation should follow the – Phase 1 (Laboratory Investigation) and Phase 2 (Full scale Investigation) process as detailed in the USFDA / MHRA guidelines for handling of OOS. The Phase 1A looks at Obvious errors and Phase 1B – Laboratory investigation evaluate possible laboratory error – sample handling, sample preparation, test method, analyst awareness, instrument malfunction and so on, with a well defined checklist. And during Phase 1B evaluation if possible laboratory errors are identified, this shall be verified through hypothesis testing – testing performed to help confirm or discount a possible root cause:- for example it may include further testing regarding sample filtration, sonication /extraction; and potential equipment failures etc. Based on Phase 1B investigation and hypothesis testing, sample shall be retested and batch disposition decision concluded. However the hypothesis should be scientifically justified and supported by the facts of the initial analysis and observations made in Phase 1B investigation checklist. For example, a proposed sample preparation error of insufficient sonication / extraction is not convincing if there were several samples tested / sonicated together but only one or two samples were OOS. The root cause is not conclusive. When the root cause is not conclusive, the OOS investigation should also be extended to Phase II, manufacturing investigation. Manufacturing investigation should evaluate manufacturing steps and adequacy, equipment and facilities, materials, operator error, deviations, history of failure. The investigation should conclusively show that the OOS could not have been caused due to manufacturing related issues. Identifying scientifically sound probable root cause helps in implementing appropriate corrective and preventive actions (CAPAs) – e.g. redefining the sonication / sample extraction process – time, temperature; glassware cleaning methods, sample handling, training the analyst for improving the analyst skills, and prevent recurrence of similar OOS. Firms should track and review trend of the OOS for recurring events; recurring OOS events show the actual root cause was not identified and whatever CAPA were documented are ineffective. This should trigger a reopening of the previous OOS events and investigation, a deep dive into the OOS incidents to establish the actual root cause.
 The test methods and procedures should be appropriately validated and all possible variables evaluated during method validation. The test methods shall document the precautions and do’s and don’ts with possible impact. Preforming only basic rudimentary method validation for documentation and regulatory filing purpose is a sure recipe for later issues during routine quality control testing.
Firms should also establish adequate Quality and Executive Management oversight. The Quality Assurance (QA) function shall review the OOS trends, identify recurring OOS and flag for revaluation. There shall be periodic management review (typically once a month) where the executive management review the performance of the Quality Management system (QMS) along with site operations team and the Quality Unit. The management review meeting shall review trends of deviations, OOS, other discrepancies and failures, recurrence of the Quality events, CAPA implementation and effectiveness. Procedure for Management review meetings with defined agenda shall be documented. Â
Also refer the posts:
  Humidity excursion deviations.
Humidity excursions in manufacturing areas can affect product quality; impact may show immediately (in batch release testing) or could manifest later during the shelf life of the product. Humidity excursions in manufacturing areas could be due to one or several causes – for e.g. (but not limited to) – issues with dehumidification system, compressor, fan, leaks in refrigerant coils, clogging of condensate lines, water drainage from system; it could also be due to other factors in manufacturing area – operator practices, frequent opening and closing of doors, leaving doors open, specific processes. Repeat excursions should trigger a full scale investigation involving a cross functional team (CFT) – Manufacturing, Engineering, QA, as the root causes could be system related, practice related, process related or a combination of several factors. Use an appropriate investigation tool – a brain storming session with Ishikawa (fishbone) analysis could be a useful tool to evaluate various factors – Men / Machine / Method / Material / Mother nature. Review the cleaning and maintenance practices of the dehumidifier system. If the corrective action identified to address the root cause need a lead time – for e.g. defect with the dehumidifier requiring major overhaul or replacement, establish interim control measures. For example – Limiting operations so that the HVAC / dehumidification systems can support the most critical areas in manufacturing and packing; temporary solutions like potable dehumidifier. Perform a risk assessment of the impact of humidity on products, identify products which require less stringent humidity controls. A temporary relaxation of limits (planned deviation or temporary change) for humidity specifications may be applied, production plan tweaked to take up products which have less humidity impact till the issue is resolved. Deviations can be handled in different ways minimising impact on production and ensuring quality & safety of products, but the key point is that deviations from prescribed conditions / specifications and processes should be identified, acknowledged and investigated promptly.
Nowadays stability chambers come with various features to alert the users in case of excursions, prevent excursions – e.g – Mobile alarm systems, standby compressors in case primary control fails, compliant software for stability chamber data management with access controls, back up, audit trails. Ensure the stability chambers have the  required controls and features / upgrade the systems. In spite of such controls, if excursions still happen, investigate the root cause– are the alarms active and working, are the standby system in place and working, is the preventive maintenance programme cover alarm functioning, verification of standby systems. is there a process in place for people to respond to alarms in time and act if excursion happen in silent hours (when regular QC, QA and other operational staff are not present say in night time / holidays). Accordingly implement corrective actions to address the gaps.
The stability chamber temperature and humidity records, and alarm data, backup status shall be verified daily. This ensure that even if excursions happen, or a data loss happen due to any hardware/software malfunction, this could be for a maximum of 12-24 hours by when the issue is noted, and acted upon. It is a good practice to take print of the stability chamber data daily, review and archive (either as paper copies or electronic copy).Â
It will be prudent for Firms to review their historical OOS events, invalidated OOS events, recurring OOS events, root cause(s), CAPAs implemented and their effectiveness and take measures to address lapses if any.
When humidity excursions happen in manufacturing area or in stability chambers, perform a comprehensive investigation to establish root cause and CAPAs. Review and enhance control features in stability chambers. Assess batches that could be affected by the humidity excursions in manufacturing area, and consequent impact on microbial quality. Reserve samples of affected batches within valid expiry shall be retested for microbial counts and where failures are observed, initiate remediation action. Review potential for humidity control failures in other manufacturing lines and areas, document the same and extend the corrective actions identified (procedural controls, preventive maintenance checks, cleaning and others) to these areas as well.
Leave a Comment
You must be logged in to post a comment.