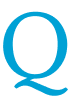
Warning letters, 483s, Recalls, Import Alerts, Audit observations
USFDA Inspection of Intas, Matoda, Sanand facility in India (FEI 3004011473); from 22 November 2022 to 12 December 2022 by FDA inspectors Jose E Melendez, Justin A Boyd, Pratik S Upadhyay, resulted in issuance of 36 page USFDA 483 with eleven (11) observations. One particularly serious observation cites Quality unit’s lack of oversight on the control and management of GMP documents – torn pieces of GMP documents (QC balance print outs, QC spectrums, Raw data, GMP documents from Production, Engineering) from site found in a truck outside the firm, hidden under the stairs in QC, scrap area. Firm’s employees from QC Production and Engineering departments deviated from core principles of Data Integrity and Good Documentation Practices.
USFDA483
Observation 3
The responsibilities and Procedures applicable to the Quality control unit are not fully followed.
There is a cascade of failure in the Quality unit’s lack of oversight on the control and management of GMP documents:
1. On 22nd November 2022 it was observed the Firms Quality Control laboratory, Production and Engineering personnel destroyed GMP documents pertaining to original records and rawdata and disposed inside QC laboratory and General Parenteral scrap areas. Additionally, a truck was found about 150 meters from the facility (the driver of truck upon interview stated it is from the Firm), waiting for clearance to remove scrap materials from SEZ with several plastic bags containing shredded and torn pieces of documents from the firm. As per Firm’s employees the disposed material found in trash areas and the truck was from 21 and 22 November 2022. Among many torn and shredded documents found inside the truck torn pieces of analytical weight slips (Balance printouts) along with spectrums pertaining to analysis of different tablet batches and capsule batches (commercialized in the USA market) were observed. Firm’s QC employees deviated from Good Documentation Practices and Data Integrity procedures by destroying “Original record” and “Rawdata”. Additionally, the Quality unit lack adequate oversight in ensuring data pertaining to drug products is complete and reliable.
a. There were no weight specific entries in the Laboratory Information Management System (LIMS) “Instrument usage logbook” for the time recorded in any of the balance printouts. Further there is no consistency among the QC employees in terms of recording of information in LIMS log book pertaining to total number of lots tested. Some QC employees enter this information, whereas others may not. This issue is applicable to all analytical Instruments in the QC laboratory including Balances, Auto Titrators, HPLCs, GCs.
The time stamp on balance printout and spectrum printout did not match with LIMS instrument usage log (Analytical Balance ID PC344; PC069). The Associate Executive Vice President of Corporate Quality & Compliance and Manager of QC confirmed stating that in a period of about 45 minutes, the Senior Officer of QC weighed out same samples multiple times and used it for tests. The rawdata pertaining to above balance and spectrum print out that has results on it were torn into pieces by hand and disposed inside plastic bags, later found by the investigator inside the truck.
b. Comparing torn pieces of print outs from Analytical Balance ID:. PC 344 and Instrument ID PC069, the inspectors observed, the Senior Officer QC weighted the same batch multiple times in an attempt to hide testing discrepancies. The verification of weights and time stamped on the spectrums did not match. The justifications provided by the Senior Officer was inadequate and as such in deviation of Good Documentation Practices and Data Integrity procedures.
c. Details of type of GMP documents (Original records and raw data) found destroyed and disposed inside scrape areas and truck with scrap materials.
i. Large plastic bag hidden under staircase in QC laboratory scrap area with torn pieces of GMP documents
ii. Trash truck with GMP documents mixed with general scrap. On 22nd November 2022 observed hundreds of transparent and black plastic bags containing torn pieces of analytical balance weight slips (Analytical balance ID. PC278 and another balance with ID missing in the paper).
iii. Torn pieces of GMP documents – around 14 black plastic bags were observed on 22 Nov 2022 in Room Number G1025 (Scrap room 06) – General Parenteral Area.
Quality unit lacked adequate oversight on documents being lost from the system, no unplanned deviations initiated to investigate root cause for missing / lost documents and to take CAPA to avoid recurrence losing documents and destruction of documents by employees. Firms employees from QC Production and Engineering departments have deviated from core principles of Data Integrity and Good Documentation Practices defined in Firm’s procedures.
2. On 22nd November 2022 found torn pieces of a document from scrap areas that upon putting together contained handwritten comments on a piece of uncontrolled and unofficial paper by a Production Reviewer. Production officer that signed this document under “Checked by/ Date” section changed number from four (4) to make it look like five (5). Production officer has deviated from Firm’s procedure for Good Documentation Practices.
3. Firm logged five (5) Unplanned Deviations (UDs) for missing / lost documents since 21st August 2020. The primary root cause identified in each of the UDs being personal error. No CAPA was taken for four out of five UDs, simply imparted awareness training to the Production employees; and decided to implement eBMR, in a phased manner, across the site. However, while implementation of EBMR Is currently underway, Firm’s employees from QC, Production and Engineering departments continued to destroy original data, raw data and metadata. Out of five UDs two events pertain to products for USA market. In both cases. Quality unit initiated no CAPA.
Observation 3
The responsibilities and Procedures applicable to the Quality control unit are not fully followed.
There is a cascade of failure in the Quality unit’s lack of oversight on the control and management of GMP documents:
1. On 22nd November 2022 it was observed the Firms Quality Control laboratory, Production and Engineering personnel destroyed GMP documents pertaining to original records and rawdata and disposed inside QC laboratory and General Parenteral scrap areas. Additionally, a truck was found about 150 meters from the facility (the driver of truck upon interview stated it is from the Firm), waiting for clearance to remove scrap materials from SEZ with several plastic bags containing shredded and torn pieces of documents from the firm. As per Firm’s employees the disposed material found in trash areas and the truck was from 21 and 22 November 2022. Among many torn and shredded documents found inside the truck torn pieces of analytical weight slips (Balance printouts) along with spectrums pertaining to analysis of different tablet batches and capsule batches (commercialized in the USA market) were observed. Firm’s QC employees deviated from Good Documentation Practices and Data Integrity procedures by destroying “Original record” and “Rawdata”. Additionally, the Quality unit lack adequate oversight in ensuring data pertaining to drug products is complete and reliable.
a. There were no weight specific entries in the Laboratory Information Management System (LIMS) “Instrument usage logbook” for the time recorded in any of the balance printouts. Further there is no consistency among the QC employees in terms of recording of information in LIMS log book pertaining to total number of lots tested. Some QC employees enter this information, whereas others may not. This issue is applicable to all analytical Instruments in the QC laboratory including Balances, Auto Titrators, HPLCs, GCs.
The time stamp on balance printout and spectrum printout did not match with LIMS instrument usage log (Analytical Balance ID PC344; PC069). The Associate Executive Vice President of Corporate Quality & Compliance and Manager of QC confirmed stating that in a period of about 45 minutes, the Senior Officer of QC weighed out same samples multiple times and used it for tests. The rawdata pertaining to above balance and spectrum print out that has results on it were torn into pieces by hand and disposed inside plastic bags, later found by the investigator inside the truck.
b. Comparing torn pieces of print outs from Analytical Balance ID:. PC 344 and Instrument ID PC069, the inspectors observed, the Senior Officer QC weighted the same batch multiple times in an attempt to hide testing discrepancies. The verification of weights and time stamped on the spectrums did not match. The justifications provided by the Senior Officer was inadequate and as such in deviation of Good Documentation Practices and Data Integrity procedures.
c. Details of type of GMP documents (Original records and raw data) found destroyed and disposed inside scrape areas and truck with scrap materials.
i. Large plastic bag hidden under staircase in QC laboratory scrap area with torn pieces of GMP documents
ii. Trash truck with GMP documents mixed with general scrap. On 22nd November 2022 observed hundreds of transparent and black plastic bags containing torn pieces of analytical balance weight slips (Analytical balance ID. PC278 and another balance with ID missing in the paper).
iii. Torn pieces of GMP documents – around 14 black plastic bags were observed on 22 Nov 2022 in Room Number G1025 (Scrap room 06) – General Parenteral Area.
Quality unit lacked adequate oversight on documents being lost from the system, no unplanned deviations initiated to investigate root cause for missing / lost documents and to take CAPA to avoid recurrence losing documents and destruction of documents by employees. Firms employees from QC Production and Engineering departments have deviated from core principles of Data Integrity and Good Documentation Practices defined in Firm’s procedures.
2. On 22nd November 2022 found torn pieces of a document from scrap areas that upon putting together contained handwritten comments on a piece of uncontrolled and unofficial paper by a Production Reviewer. Production officer that signed this document under “Checked by/ Date” section changed number from four (4) to make it look like five (5). Production officer has deviated from Firm’s procedure for Good Documentation Practices.
3. Firm logged five (5) Unplanned Deviations (UDs) for missing / lost documents since 21st August 2020. The primary root cause identified in each of the UDs being personal error. No CAPA was taken for four out of five UDs, simply imparted awareness training to the Production employees; and decided to implement eBMR, in a phased manner, across the site. However, while implementation of EBMR Is currently underway, Firm’s employees from QC, Production and Engineering departments continued to destroy original data, raw data and metadata. Out of five UDs two events pertain to products for USA market. In both cases. Quality unit initiated no CAPA.
Companies should nurture a strong Quality culture in the organization with several elements – Quality and Management oversight, Zero tolerance for Data Integrity, Internal Compliance audits, Instruments and systems with electronic data compliance, Comprehensive Quality system procedures with checks & cross checks. Strengthen the quality culture and values which promptly acts on any practices which compromise integrity such as but not limited to Generation of data (like weighing same sample multiple times), Hiding and attempts to Destroy raw data, Unofficial records. An R&R (Rewards &Recognition) system which encourages compliance and Integrity at all levels, Coaching and Mentoring of personnel. Specifically,
All analytical instruments including stand alone systems like Analytical Balances, Auto Titrators should have Date &Time locks where in no user level changes are possible. As much as possible all analytical instruments to be controlled through secure and compliant computer systems.
Ensure consistent practices in documentation, logging (date, time, when to log, how to document). Rather than only having SOP and training, take up workshops for such GMP practices to discuss and review how personnel handle, identify areas for streamlining and synchronization.
Procedure for alarms handling should be part of the operational SOP for all GMP critical equipment and instruments which generate alarms. Alarms may be categorised as Critical / Major / Only for alert (information) & actions required to be taken against different alarms should be listed. Equipment and systems should ideally have an alarm log with traceability to the activity performed (such as a sample set analysis). Review of the test and results should include a review of the alarm log of equipment’s involved. A print of the alarm log can be taken and reviewed and the same can be filed along with test results; alternatively use an alarm review checklist. Typical alarm review documentation will show there was no abnormal events / alarms or in case of any abnormal critical alarms, the actions that were taken, impact assessment and conclusion. (Similar procedure for alarm handling should be implemented for other GxP equipment & systems as well – e.g. manufacturing equipment, HVAC systems etc).
Complete control on documentation in all areas. No uncontrolled papers and documents, whether it is a trial, evaluation or GMP operation (“Unofficial Documents!!). Any evaluations /activities performed to be documented through controlled documents even if it is only for data collection, however inconsequential or trivial the data is and archived in a traceable manner with appropriate comments. This is much better than documents with data being picked up from somewhere -scrap areas, trash cans, cupboards and so on. Ensure a zero tolerance approach towards any violation across all levels.
Any piece of GMP document, any original print out taken, archive with associated parent document (e.g.: additional print since first one was illegible or a print taken with wrong set of parameters) with comments. Avoid taking prints and making notes on the prints unless it is absolutely necessary and is a requirement of the procedures.
Have a complete control on scrapping of GMP documents including shredding of documents through paper shredders. Document destruction should be a controlled activity with authorization from Quality unit and logs maintained. Document shredding machines (shredders) should also be controlled with logbook and documentation of shredding activities performed. Document archival and storage locations, scrap areas should be well defined with access controls. The observation of truck with torn GMP documents can have an industry wide impact with additional audit check points for regulatory auditors. It is worth considering having a defined and controlled system to control storage and movement of scrapped documents.
Be audit ready at all times. No accumulation of materials, documents in any areas especially scrap areas, however justifiable it is. Such material invite attention, and inspectors are wary of such areas, suspicion creeps in and the inspection takes an unpleasant turn to investigation. And once the regulatory audit or inspection become an investigation panic sets in, people flounder.
Quality unit should have the freedom and authority to ensure prompt Quality actions are taken when Quality events occur. Especially during audits (even otherwise as well), when any discrepancy / deviations from systems, procedures, GxP is observed, log a Quality event (typically unplanned deviation) and initiate investigations. This shows a positive attitude of a company and the Quality unit; Mistakes may happen despite the best efforts, but then what matters is how the people and the organisation responded to it.
Inspectional Observations as cited in the 483 require a Comprehensive Review of systems, procedures, practices, personal practices, personal capabilities and personal competencies, gaps in GMP compliance of instruments and equipment (21 CFR Part 11 compliance). It is prudent to engage an outside GMP and compliance expert for comprehensive evaluation, investigate what all areas & products will be impacted and identify measures to be taken. Products and Batches potentially impacted will need to be promptly recalled, unless there is a strong justification and evidence for not doing the same. Review of personal capabilities and competencies and revamping of the organization with redeployment / redesignation of personnel, coaching and training and nurturing a Quality Culture will need to be taken across organization. Based on the review and evaluation establish a comprehensive CAPA plan addressing GMP and Quality systems, Practices, Procedures, Personnel, Equipments and Instruments, Control of GMP documents including scrap, Quality and Management oversight and enhanced vigil and survelliance. The observations is also a strong case for moving to electronic documents and control in place of paper documents and control in as many areas as possible.
Leave a Comment
You must be logged in to post a comment.