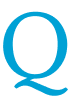
Granules India received a warning letter from the USFDA in February 2025. This was along expected lines after significant violations were observed by USFDA investigators during an inspection at the Gagillapur Village facility (FEI 3004097901) of Granules India in August-September 2024. Major observations cited in the warning letter included poor facility maintenance, damaged HEPA filters and compromised filter integrity, accumulated residues, and microbial contamination in the air supply ducts, raising concerns of contaminated air being supplied to critical manufacturing areas and equipment. The auditors also observed data integrity (DI) issues with several bags of torn cGMP documents containing manufacturing and testing data. The site was inspected by FDA auditors Pratik S. Upadhyay and Joseph A. Piechocki.
Failure of Contamination Control Systems
The observations connect lapses in three areas, raising concerns over overall contamination control systems.
In its response to the FDA, Granules India contended that it analyzed control (reserve samples) and performed an impact assessment. Based on maximum allowable carry-over (MACO) calculations, the risk to drug product safety is low; Firm also provided assurance of low microbiological contamination risk to products. Birds were entering the facility through numerous gaps in the exterior wall of the facility, and the Firm proposed to block the entry points with nets. Granules India confirmed damage to filters, increased pressure differentials, and proposed to monitor pressure differentials to determine when cleaning or replacement of filters is required.
cGMP Records and Data Integrity Issues
Large amounts of torn cGMP records, including analytical balance printouts and manufacturing/testing data, were observed in waste bags. The Form 483 observed employees recording data on uncontrolled white paper and disposing of GMP documents and records like analytical instrument printouts and other raw data documents.
Granules India provided supporting documentation to show that the deviation did not affect product quality and identified several root causes, including lack of clarity in documentation practices and data integrity protocols, inadequate SOPs, employee misinterpretation of requirements, failure to archive defective and illegible printouts, and lack of control over raw data sheets. However, the FDA contended that the firm’s quality system does not ensure accuracy and integrity of data.
The FDA found the responses of the Firm inadequate in several respects. FDA’s objections included:
Some Key Learnings
The warning letter highlights several key issues to be addressed while handling critical deviations.
Leave a Comment
You must be logged in to post a comment.