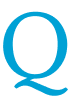
Warning letters, 483s, Recalls, Import Alerts, Audit observations
USFDA inspection of Cipla, Patalganga site manufacturing APIs and Tablets resulted in USFDA 483 with six observations. The facility (FEI 3002806710) was inspected by USFDA inspectors Lori M. Newman, Sean R. Marcsisin in March / April 2024. The 483 highlighted deficient cleaning and maintenance with observation of spots and residues in cleaned equipment and flying insects in an equipment bowl in the manufacturing area (ISO-8) which further led to observation of gaps in duct seal and sealant debris in duct. OOS investigations and root cause were found inadequate with repeat particle size variation OOS incidents in an active pharmaceutical ingredient (API). Equipment Qualification practices were found deficient as an equipment was put into use without performing risk assessment or equipment qualification. Deviations during packing of API are not documented and evaluated. Procedures are not fully followed by Quality unit, samples were not send to QC as required by procedures when alarms are sounded by system indicating high value for operating parameter.
Qvents discusses the cGMP practices, controls to be in place in the backdrop of the USFDA 483 and corrective actions (CAPAs) to be taken when deviations happen.
Flying insects were observed in a bowl in a manufacturing area (ISO 8). The clean room duct was inspected (on 3 April 2024) and observed several external damages to the duct, a large gap in the duct seal big enough to allow a 11 x 8 inch paper to be inserted. The duct seal was not integral and the Firm was not aware of the breach. Sealant has been used in the duct to seal around the duct gasket and the sealant debris and other debris were observed inside the duct. Firm not aware when the sealant (caulking) is applied and why. During the last preventive maintenance (February 2024) gasket / seals are documented to have been inspected; at least one technician involved in the PM didn’t have evidence of training.
Instill the right Quality culture in people, encourage personnel to report events, record and investigate the events and establish the root cause. Develop the capability in the team to connect issues – as the FDA auditor did when observation of insects led the auditor to the clean room duct,. Another fundamental GMP practice is to ensure documentation of activities and events. This helps in defining the scope and extent of investigations and remediation actions. Also when deviations are identified, the investigations and corrective actions need to be comprehensive and CAPAs global. Review and verify all similar systems, identify gaps if any and take corrective actions.
During inspection observed spots, white residues on bolt, shaft of equipment, which are exposed to drug product discharge flow path, on equipment with “Clean” status. An equipment cleaning and operation SOP provided for repeating the cleaning procedure if any residue are observed during verification until results are satisfactory; It was found to be lacking to trigger an investigation in case of failed cleaning. For example, as per cleaning log of an equipment, when powder was observed in a duct during verification after cleaning the ducts were recleaned with no investigation as to why cleaning was initially insufficient.
Written procedures shall be established for cleaning and validation of the cleaning procedures and cleaning procedures validated (Refer 21 CFR 211.67, USFDA Guide to Inspections: Validation of Cleaning Processes). When a cleaning failure occur, there need to be in investigation to identify what steps of a cleaning process caused failure, evaluation of effectiveness of the cleaning process, identification of gaps / root cause and address the same through adequate CAPAs. A cleaning process which is designed to clean till no residues are observed do not give an assurance of the process.
OOS incidents are not holistically investigated to ensure all factors that contribute to repeated OOS incidents in Particle Size distribution of an API are identified and remediated. Observed eight OOS incident on particle size distribution of an API from 2020 to 2024
Repetition of same/similar OOS events (eight times from 2020 to April 2024 as shown in the example) clearly indicate that the real cause is not yet established. The OOS events should be investigated thoroughly using appropriate tools, for e.g. Why-Why analysis to get at the root cause. Also review historical trend of OOS to identify recurring OOS and evaluate adequacy of CAPAs taken.
An equipment acquired to help during operations to address Particle size OOS events was put into use without performing a risk assessment or performing equipment qualification. This was a requirement of the Firm procedure.
USFDA GMP requirements mandate that the equipment used for cGMP activities shall be of appropriate design for its intended use. (USFDA 21 CFR 211.63). This is demonstrated by Equipment Qualification. Perform GxP risk assessment of the Equipment and instruments, evaluate the GxP criticality of the equipment, whether the equipment or system can impact product quality, safety. If yes qualify the equipment to demonstrate it perform consistently, reliably, and according to established specifications (ISPE Guidelines on Equipment Qualification).
All deviations during packing of Active Pharmaceutical Ingredient (API) are not evaluated.
Recording deviations, evaluation and investigation to identify root cause and establish CAPAs to prevent recurrence of deviations is fundamental to Pharma GMP.
Following stopping of a system due to high value for a control parameter and system sounding alarm, samples were not send to QC for verification as required by the Firm’s procedure.
For all GxP systems (Water system, HVAC systems, Air / Nitrogen, Production equipment and so on), critical alarms and actions to be taken when alarms are sounded shall be defined, records including action taken records shall be maintained. Operating personnel shall be well trained in the procedures to ensure that they are followed in all situations.
Leave a Comment
You must be logged in to post a comment.