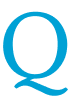
Warning letters, 483s, Recalls, Import Alerts, Audit observations
USFDA 483 / IPCA Laboratories, Silvassa, India / FEI 3005977675/ USFDA Investigators: Rajiv Srivastava, Kellia Hicks / Inspection dates April 18-26, 2023 / Observation 1 – Deficiencies in failure investigations (OOS, Complaints)
USFDA 483 to IPCA, Silvassa (April 2023) cites inadequacies and lack of thoroughness in Out of specification (OOS) investigations, complaint investigations. In OOS investigations, when root cause identified is probable laboratory error, a manufacturing investigation necessarily need to be performed. When only probable root causes are projected in failure investigations, adequate rationale should be documented how other possible factors are discarded. In this post Qvents is reviewing the Observation 1 in the Form 483
Failure to thoroughly review any unexplained discrepancy and the failure of a batch or any of its components to meet any of its specifications.
Specifically,
OOS
A. Firm failed to follow validated analytical method for test of Assay by HPLC and failed to conduct a complete investigation as per the established OOS procedure.
An OOS is reported for a batch of tablet with assay lower than the specification limits. Phase I investigation did not reveal any assignable root cause. Firm proceeded to Phase IIB investigation, without conducting the Phase IIA manufacturing investigation. Two batches were analysed in the same sequence in the hypothesis testing. Based on the higher assay results obtained with a non-validated method, firm concluded root cause. There was no sound justification while concluding the root cause why it will cause a lower value of assay for the OOS batch and not the passing batch. (The incident referred is a Non.U.S tablet batch).
B.Firm invalidated OOS result without scientifically justified root cause.
An OOS was reported in a batch of tablets for lower assay. Phase I investigation did not reveal any assignable root cause and no deficiencies noted in the sample preparation. A hypothesis testing was performed to prove a proposed root cause for the OOS, which resulted in two completely different (results). Firm used the probable root cause to retest the new sample and based on the passing assay value invalidated the initial OOS result. (The product is a batch of tablets, a Non U.S. Batch)
 OOT
C. Firm failed to follow validated analytical test method & complete investigation as defined in OOT procedures
An OOT result was reported for lower essay in a tablet batch. Phase I investigation did not identify any assignable cause. Firm proceeded for Phase IIB without conducting a Phase IIA manufacturing investigation. Based on the higher assay result with a non validated method, during Phase IIB investigation, the probable cause for the OOT was concluded. There is no scientific justification of the root cause for the lower assay result of failing batch (OOT), while there are passing batch(es) as well. Firm retested the batch and invalidated the initial OOT result. Firm also failed to follow the defined OOT procedure; manufacturing investigation (Phase IIA) was not performed.
Complaint Investigation
D. Firm received complaint for a spot on tablet and root cause was attributed to API. However, the Firm failed to establish the connection between the API manufacturing process and the presence of spot in the finished product. Investigation report stated the manufacturing operations are in Grade D (ISO 8) conditions. However, Firm failed to document how it ensures adequate exhaust system to control contaminants in areas where contamination can occur during production & Firm did not evaluate data to verify room classification for Grade D (ISO 8) area. The product & batch is a Non US Batch.
Failure to thoroughly review any unexplained discrepancy and the failure of a batch or any of its components to meet any of its specifications.
Specifically,
OOS
A. Firm failed to follow validated analytical method for test of Assay by HPLC and failed to conduct a complete investigation as per the established OOS procedure.
An OOS is reported for a batch of tablet with assay lower than the specification limits. Phase I investigation did not reveal any assignable root cause. Firm proceeded to Phase IIB investigation, without conducting the Phase IIA manufacturing investigation. Two batches were analysed in the same sequence in the hypothesis testing. Based on the higher assay results obtained with a non-validated method, firm concluded root cause. There was no sound justification while concluding the root cause why it will cause a lower value of assay for the OOS batch and not the passing batch. (The incident referred is a Non.U.S tablet batch).
B.Firm invalidated OOS result without scientifically justified root cause.
An OOS was reported in a batch of tablets for lower assay. Phase I investigation did not reveal any assignable root cause and no deficiencies noted in the sample preparation. A hypothesis testing was performed to prove a proposed root cause for the OOS, which resulted in two completely different (results). Firm used the probable root cause to retest the new sample and based on the passing assay value invalidated the initial OOS result. (The product is a batch of tablets, a Non U.S. Batch)
 OOT
C. Firm failed to follow validated analytical test method & complete investigation as defined in OOT procedures
An OOT result was reported for lower essay in a tablet batch. Phase I investigation did not identify any assignable cause. Firm proceeded for Phase IIB without conducting a Phase IIA manufacturing investigation. Based on the higher assay result with a non validated method, during Phase IIB investigation, the probable cause for the OOT was concluded. There is no scientific justification of the root cause for the lower assay result of failing batch (OOT), while there are passing batch(es) as well. Firm retested the batch and invalidated the initial OOT result. Firm also failed to follow the defined OOT procedure; manufacturing investigation (Phase IIA) was not performed.
Complaint Investigation
D. Firm received complaint for a spot on tablet and root cause was attributed to API. However, the Firm failed to establish the connection between the API manufacturing process and the presence of spot in the finished product. Investigation report stated the manufacturing operations are in Grade D (ISO 8) conditions. However, Firm failed to document how it ensures adequate exhaust system to control contaminants in areas where contamination can occur during production & Firm did not evaluate data to verify room classification for Grade D (ISO 8) area. The product & batch is a Non US Batch.
It is interesting and important to note that the batches mentioned in the 483 are all non-U.S.batches; shows that auditors focus is about the OOS procedure (SOP) and investigation process, irrespective of whether the batches involved are for US or not.
The observation, points several key aspects Companies should take care while handling OOS investigations.
One most important point is that when root cause is not clearly established, and only probable root cause of laboratory errors is projected, there has to be a Manufacturing investigation performed. Only when the manufacturing investigation has clearly established (and documented), that there is no deviations or discrepancies in the manufacturing process which can cause an OOS, the probable root cause of a laboratory error has credence.
Another important point to note is that in analytical validations, the robustness of the method should be clearly evaluated. For example, if it’s an assay method all the potential factors that can impact the result – sonication time, time for which sample should be shaken to ensure complete extraction of the active ingredient from the sample matrix, whether tablets should be crushed and taken or taken as such….and so on should be evaluated. Precautions to be taken during analysis should be documented in the method, analysts trained in the same. It does not help to perform only basic rudimentary validation for documentation and regulatory filing purpose. It does not give confidence to auditors when there are repeated instances of issues with analytical method, cited as probable root cause. It makes things harder, when in the same analysis sequence, there are both passing and failing results. There should be sound evaluation and rationale to explain why only some batches are affected due to lapses In the method or execution of the method – the ones with failing results, while there are passing results as well in the same analytical sequence or set. Also the investigation process of Phase IA (checking for obvious errors), Phase IB (detailed laboratory investigation) should be performed judiciously. The hypothesis testing in Phase II (extended investigation), should draw from Phase IB investigation. For example, if there is a checkpoint for sample preparation in Phase 1B checklist which is ticked as sample preparation was appropriate, there is no rationale for doing a hypothesis testing on sample preparation errors during Phase II investigation. Rather the checkpoint and document can indicate, even when even when apparently the sample preparation looks fine, what possible issues can happen during execution of the method. Then such gaps can be checked out during Phase II extended investigation, by hypothesis testing – but only after a manufacturing investigation confirms there are no assignable causes from manufacturing process. The Phase IA, IB checklists should be updated and reviewed by knowledgeable, experienced Quality personnel who can visualize probable errors that can happen and indicate the same in the investigation checklists, rather than reducing it down to a routine checkbox ticking exercise.
In complaint investigations (as well as other deviations and failure investigations) also, when a root cause attributed is a probable root cause, the rationale should be sound and documented. Also the investigation documentation should discuss, why other possible causes are discarded. In product complaints, product failure investigations etc often the input material gets identified as source of issue. In such cases Investigation documentation should also discuss how input material controls (like QC testing) could not identify and prevent the issue, CAPA should address this aspect as well. Without this the investigation documentation looks shallow and superficial.
As a learning from the cited observations in the above 483, Quality Units of Companies can review whether similar situations exist in their site. Review the historical OOS data (all invalidated OOS batches within expiry) to see instances of Invalidated Out of specification (OOS) where a clear root cause is not established and probable laboratory error is attributed to the OOS result. Review whether a manufacturing investigation has been performed in such cases. If not, those OOS Investigations may be reopened and reviewed on current date, manufacturing investigation performed and documented as an addendum. This can be done for example as part of a continuous improvement program or a QRM program. Similarly review invalidated OOS with laboratory error as probable root cause, whether in the analysis sequence there are both passing and failing batches; and adequate rationale is documented in such cases why some of the batches passed. If this is not done, address the same on current date and update as addendums. If there are gaps or new issues identified in such reviews, address the same.
Review the OOS procedure and checklists in line with USFDA / MHRA guidelines for handling of OOS, specifically addressing requirement of manufacturing investigation where root cause is not clearly established and probable root cause is identified as laboratory error. Train and coach the personnel in appropriate implementation of the OOS procedure, Phase 1A and Phase 1B laboratory investigation and manufacturing investigation.
Review the analytical methods, method validations, see whether the precautions to be taken while executing the method are adequately documented, whether the analytical methods, are practiced as documented. Address the gaps, If any.
Similarly, review the historical complaint investigations data to see whether clear and assignable root causes are identified for the complaints/failures. Where only probable causes are projected, review whether all other factors which can cause the failure are evaluated, and documented. If not, perform an assessment on current date and document as addendums. Take adequate actions to address identified gaps if any.
Leave a Comment
You must be logged in to post a comment.