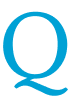
Warning letters, 483s, Recalls, Import Alerts, Audit observations
USFDA Warning letter to Dupont cites inadequate change management program. The warning letter to Dupont Nutrition USA in December 2022 for site at Newark, Delaware, USA ( (FEI 3013947845) followed an USFDA inspection during November and December 2021 and inadequate response to inspection observations by Dupont. The site manufacture the Pharmaceutical excipient Avicel (Microcrystalline cellulose)
Failure to have an adequate change management program to evaluate and approve changes that may impact the quality of the excipient.
Â
Avicel process performance qualification studies conducted from 2001 through 2007 identified conductivity as a critical quality parameter. However, in approximately 2011 firm removed the conductivity meters without a documented change control.
Â
Firms response stated that at the time of the change potential impact on the quality of Avicel was evaluated, but did not document this evaluation. Firm also state it will evaluate the impact of any other process changes implemented without adequate review on the quality of your excipient. Firm also committed to evaluate process changes for potential impact on other critical quality parameters listed in the most current validations (dated 2001, 2004, and 2007). However, a detailed plan or timeline for implementation of the revised change management program is not provided.
Â
In response to the Warning letter, Firm to provide:
A comprehensive, independent assessment of change management system. This assessment should include, but not be limited to, procedure(s) to ensure changes are justified, reviewed, and approved by quality unit. Change management program should also include provisions for determining change effectiveness.
Â
A remediation plan that better assures ongoing management oversight throughout the manufacturing lifecycle of all excipients. Provide a more data-driven and scientifically sound program that identifies sources of process variability and assures that manufacturing (including both production and packaging) operations meet appropriate parameters and quality standards. This includes, but is not limited to, evaluating suitability of equipment for its intended use, ensuring quality of input materials, determining the capability and reliability of each manufacturing process step and its controls, and vigilant ongoing monitoring of process performance and product quality.
As can be seen from the FDA warning letter manufacture of Excipients need to comply with applicable cGMPs as per 21 CFR 210&211 and other applicable regulations just as the drug product and drug substance manufacturers.. Companies should have comprehensive change management (change control) procedure addressing:
Work out a detailed action plan with timelines for completing all the actions identified. Keep track of all above actions. Provide FDA a comprehensive response and periodic updates on the progress of actions.
Leave a Comment
You must be logged in to post a comment.