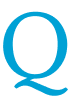
Warning letters, 483s, Recalls, Import Alerts, Audit observations
USFDA Warning letter  to Centrient India (Toansa, Punjab FEI 3004497364) in December 2022 cited deficiencies in
investigating critical deviations like black particles product, inadequate CAPA. Warning letter followed USFDA inspection at Centrient India site in June-July 2022.
Failure to establish and follow written procedures for investigating critical deviations or the failure of API batches to meet specifications.
Failed to adequately investigate and determine the root cause of black particles in two batches of API. Investigation report stated the black particles were non-metallic charred product residue, but failed to provide data to support the conclusion.
Firms response indicated installation of (system) to limit presence of metal particles. However, investigation remains inadequate because, firm did not provide the data to support proposed root cause or identify an adequate CAPA. The CAPA does not address non-metallic sources of contamination such as charred product residue or inadequate cleaning or fully address metallic sources of contamination such as reactive, additive, or absorptive product contact surfaces.
Firm to provide:
A comprehensive assessment of overall system for investigating deviations, discrepancies, complaints, out-of-specification (OOS) results, and failures. To provide a detailed action plan to remediate this system – significant improvements in investigation competencies, scope determination, root cause evaluation, CAPA effectiveness, quality unit oversight, and written procedures. Address how your firm will ensure all phases of investigations are appropriately conducted.
Investigation of Quality events, identification of root cause and CAPA and documentation should be sound and comprehensive. The investigation conclusions need to be objective (how a conclusion like the black particles in API is non metallic charred product residue is made, and what is root cause for such non metallic black particles, and if the black particle is non metallic charred residue what are the CAPAs for preventing such particles). The CAPA should address the root cause and root cause should be an outcome of investigation. (A system to prevent metallic particle contamination may be good to have, but this do not address the specific issue cited in the investigation and hence the CAPA will not be effective to prevent recurrence of the issue).
Â
The investigations should target to identify the root cause and establish CAPA for preventing recurrence. For example, if the cause for black particles is charred product residue, what is the cause for formation of charred residue and what actions are necessary for preventing the same (Why -Why analysis).
Â
FDA has flagged competency for investigation and overall systems and procedures for investigation of all quality events.
Â
Leave a Comment
You must be logged in to post a comment.