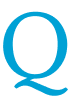
Warning letters, 483s, Recalls, Import Alerts, Audit observations
The DRL site was inspected by USFDA (Investigators Saleem A Akhtar & Pratik S Upadhyay) in October 2023. Dr.Reddys site at Medchal, Telengana (FEI 3002949099) was issued USFDA 483 with 10 observations with major observations on cleaning deficiencies, poor building maintenance. Other observations include lapses in microbiology analysis, quality control, personnel gowning, complaint handling.
In this post Qvents review the observations 1, 2 and 9 on deficiencies in cleaning and maintenance.
Observation 1
Deficient cleaning practices, presence of actives from previously manufactured products on swab samples from floor & equipment surface and in tablet samples.
Observation 2
Observation 9
Observation 1
Deficient cleaning practices, presence of actives from previously manufactured products on swab samples from floor & equipment surface and in tablet samples.
Observation 2
Observation 9
Observation of residues in equipment, products and microbial growth in manufacturing area and deficient cleaning practices are critical findings. When such issues are identified, corrective and preventive actions (CAPAs) should address comprehensive improvements in systems – enhancing the cleaning procedures, practices, fix accountability for the lapses, redeploy – replace – retrain personnel. Equally important is assessing the impact on products in the market and take market actions to stop further availability of the impacted products to patients (e.g. recall).
For a comprehensive impact assessment and evaluation of extent to which products are impacted make a protocol based assessment; For e.g.:
For incidents like microbial growth underneath equipment, mounting platform etc, perform a risk assessment for evaluating extent of impact. Review the environmental monitoring trend data, pressure cascading, differential pressure recording data. If the data support that there has been no significant changes, incidents, increase in the microbial counts and trends it could be rationalised that risk for impact on product is low. But if the environmental trend data are erratic, inconsistent with occasional spikes etc., impact on product quality and risk to patients need to be further evaluated; reserve samples analysed for any microbial excursions and accordingly and further actions (like recall) shall be taken.
CAPAs shall address comprehensive enhancement of procedures for cleaning, cleaning verification, checklists as described in previous section and training of teams. Operating personnel shall have adequate understanding of the procedures and their responsibilities. They should also have authority and should be empowered to initiate actions when deficiencies are observed – like raising maintenance notification, documenting an incident or deviation. CAPAs shall also address redeployment, replacement of personnel lacking GMP compliance, skills and aptitude.
Leave a Comment
You must be logged in to post a comment.