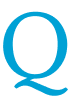
Warning letters, 483s, Recalls, Import Alerts, Audit observations
Dr.Reddy’s Laboraties (DRL) site was inspected by USFDA (Investigators Saleem A Akhtar & Pratik S Upadhyay) in October 2023. The site at Medchal, Telengana (FEI 3002949099) was issued USFDA 483 with 10 observations. The 483 lists multiple lapses in Quality control area – failure to investigate and take timely action for stability failures, inadequate investigation of unknown peaks in chromatograms, calibration failure of QC equipment. Other observations in the USFDA 483 include major deficiencies in cleaning procedures and practices, equipment maintenance, lapses in microbiology analysis, personnel gowning, complaint handling.
In this post Qvents review the observations 4&5 pertaining to lapses in Quality control area.
Access the USFDA 483
Key Deficiencies and Observations
Observation 4: Failure to investigate deviations and unexplained discrepancies thoroughly and take timely action.
For stability failure observed in 18month stability time point in September 2020 in multiple batches, the OOT logged was confirmed as “Valid” only in January 2021. Batch failure (OOS) was concluded and FAR (Field Alert Report) filed only in March 2021 after expiry of product. Also multiple failures were logged in single OOT investigation, thus under reporting the number of OOTs. The delay in the OOS investigations and conclusion (around 6 months) meant the OOS batches were still available for customers to purchase and batches were not recalled from market. The FAR was closed with no impact assessment, no corrective actions to prevent such events in future.
Inhibit integration feature (which is only to inhibit peaks from blank, placebo in sample chromatograms) applied for unknown peak in an enantiomeric purity analysis chromatogram. The unknown peak was absent in blank and system suitability injections. No investigation was performed to identify the unknown peak in the sample; the peak was not observed historically during method validation and qualification of working standards.
Observation 5: Deficiencies in calibration and preventive maintenance (PM) programme of laboratory equipment.
What companies can do to avoid such observations
Log each OOS/OOT separate: Procedures for handling OOS / OOT incidents should define how the incidents need to be reported. When OOT/OOS are reported in multiple samples analysed in a single sequence, each should be logged as a separate OOT /OOS and investigated. Root causes could be different for each incident, which will be revealed only in a investigation of each incident.
Stability OOTs/OOS: When OOT results are reported in stability analysis, that too closer to expiry (for e.g OOT reported for 18M stability time point, when expiry is 24M), there shall be an assessment of possibility of failure of the batch (OOS) before expiry; for remaining shelf life period, the frequency of analysis of the batch may be increased (for e.g 20M and 22M time points). Procedure for handling of OOT/OOS incidents shall make this explicit, and shall be part of the OOT/OOS impact assessment checklist. The objective is to avoid possibility of a failed batch to be available in the market. When OOT / OOS are reported during stability, investigation and closure of the events should get maximum priority. If investigations are not getting concluded and is going to takes time, FAR shall be filed without delay and market actions like recall may be initiated as a matter of abundant precaution.
Unknown peaks: Observation of any unknown peak in a chromatography analysis should trigger a quality event and investigation even if it is a test for specific attributes like Enantiomeric purity. Investigation shall look at (but not limited to) other analytical data – for e.g assay, organic impurities, factors such as sampling, glassware, reagents involved in analysis, sample preparations, historical data. If all aspects investigated negate possibility of a quality issue of the batch, a reanalysis and invalidation of the incident may be justified; but not investigating the incident may result in missing important quality trend pointers. Also based on possible causes identified for the unknown peak, CAPAs need to be implemented to avoid recurrence. Ensure adequate and scientifically sound robustness studies during method validation to identify all possible factors which can impact analysis – for e.g. evaluation of alternate grades of reagents, sample hold times etc. Performing only rudimentary robustness studies (like flow rate or mobile phase composition) may not reveal all possible factors impacting the analysis. Based on this ensure the test procedure have clear instructions for precautions in analysis.
Calibration & Preventive Maintenance: It is a good practice to have a preventive maintenance (PM) programme for QC equipment. The calibration / performance verification check after the PM ensure that the equipment is set properly and is performing as required after the PM. However to give assurance the instrument has been performing adequately between the last calibration and the PM activity, a performance verification before PM is a must. Any failures observed during performance verification check should be investigated; impact on batches analysed in the interim period (calibration cycle) assessed. Address the same in related SOPs – Preventive Maintenance of QC instruments, Procedure for handling calibration failures or out of calibration incidents of Instruments.
What all actions to be considered for CAPA:
When lapses in investigations of stability failures and delays, unknown peaks in chromatograms, impact assessment of calibration failure etc are identified, the CAPAs should address assessment of specific incident and impact as well as past history of similar incidents and impact on distributed batches (batch failure).
Along with enhancement of procedures, ensure appropriate checkpoints are included in the checklists for:
Train the team in the enhanced procedures, checklists and their implementation.
Leave a Comment
You must be logged in to post a comment.