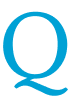
Warning letters, 483s, Recalls, Import Alerts, Audit observations
Biocon Visakh (Biocon Biosphere Limited, FEI 30221 25340) was inspected by USFDA investigator  Brandy N Lepage in June 2024. The USFDA Form 483 issued at the close of inspection observed three deficiencies. Absence of protocol driven Equipment Performance Qualification, Use of Intermediate beyond holdtime and Deficiencies in validation of Microbiological enumeration method.
Major deficiency was observed in the Equipment Performance Qualification which lacked protocol with preapproved acceptance criteria and a summary report that determine whether the equipment qualification is achieved. And Process Validation was performed on equipment which were not fully qualified following IQ/OQ/PQ. Second observation involve failure of Quality unit to investigate impact of using intermediate that exceeded established hold time in the manufacture of API. Analytical method validation of test methods for Microbiological enumeration was found deficient as it did not include the strain Aspergillus brasiliensis, failed to access suitability of the method and the growth promotion capabilities of the media to detect presence of Molds.
Learnings
1.     Process Validation/Process Performance Qualification (PPQ) and Equipment Performance Qualification (PQ)
It is common in the industry to consider Process Validation in lieu of Equipment PQ. The PICS Guide to GMP, Annex 15 – Qualification and Validation also advocate it is appropriate to perform PQ in conjunction with OQ or Process Validation. However, the point to remember is that Process Validation is to confirm the process design and demonstrate that the commercial manufacturing process performs as expected (USFDA: Process Validation: General Principles and Practices). Process validation demonstrates that the defined control strategy including raw material specifications, in-process controls, process variables (e.g. temperature, pressure, mixing time or stirring time etc.) ensure product quality throughout the process lifecycle. When all these attributes are within defined range and process gives consistent output, the Process is considered validated.
The purpose of Performance Qualification (PQ) of an Equipment is to verify and qualify that the Equipment is performing as designed while under load of the manufacturing process of the products. This can even be performed along with Process Validation or better still during execution of a scale up batch. Data on equipment performance obtained during Process Validation / scale up batches (e.g., stirrer speed, current drawn during operation, temperature, pressure, heating rate, cooling rate etc.) can support Equipment PQ. The data demonstrate the equipment operates within the specified parameters under the load of manufacturing process. To evaluate and document equipment PQ, define protocol to measure appropriate equipment performance parameters and evaluate against predefined criteria. Compile the PQ report and conclude whether the equipment is performing as defined while handling the specific product and process. Similarly monitor the equipment performance covering all different products, document the data. Capture the approach for Equipment PQ in the SOPs for Qualification and Validation.
Both Process Validation and Equipment Performance Qualification are essential components of Process Qualification. While Process Validation ensures the overall process is capable and controlled to produce quality products consistently, equipment PQ focuses on the individual equipment’s ability to perform reliably within specified parameters, supporting the process.
Other Deficiencies
 2.     Using Intermediates in Production beyond the established hold time period:
Purpose of Hold time studies is to establish the safe duration for which an intermediate can be used in the production of the final product without compromising quality. It establishes time limits for holding the materials such that the material will remain within the defined specifications. Initially, conservative hold times (e.g., 1 month, 3 months) are proposed when information is limited about the stability and characteristics of the intermediate. As more data is generated, hold times may be extended. Due to production exigencies or other reasons when intermediates beyond their established hold times are used for conversion to next stage without proper evaluation it undermines the purpose of hold time studies. Valuable insights of the material characteristics for e.g. impurity buildup, changes in flow properties and so on is missed when hold time study analysis are skipped or data not evaluated. Ensure analysis of the hold time study samples even if an intermediate exceeding its hold time is used in production, compare quality parameters between initial and hold time analyses to identify emerging trends. Before releasing the final product, review both the final product analysis results and the intermediates’ initial and hold time analyses. This holistic approach provides valuable information about intermediate stability and also help in extending intermediate hold times. (Also refer: General guidance on hold-time studies, Annexure 4: WHO Expert Committee on Specifications for Pharmaceutical Preparations)
3.     Validation of Microbiology Test Methods:
Validation of Microbiology test methods must demonstrate that the method is able to detect the microbial contamination and suitability of media with test organisms including Aspergillus brasiliensis (ATCC 16404) or equivalent (Also refer: <USP 61> Microbiological Examination of Nonsterile Products: Microbial Enumeration Tests)
Leave a Comment
You must be logged in to post a comment.