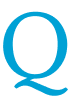
Warning letters, 483s, Recalls, Import Alerts, Audit observations
USFDA 483 to Sunpharma, Mohali unit in Aug 2022 cites deficiencies in Product Quality Reviews (APQRs), Process capability Index (CpK) indicating poor consistency, process parameters are not revised based on current data. Companies should select appropriate statistical tools for different parameters for Process and Product Quality Review rather than take a one shoe fits all approach (CpK may not be a right tool for many process parameters due to multiple contributors for variability). Companies should have systems to review effectiveness of CAPAs and Changes taken up and this should be addressed in Product Quality Review as well. Product Quality Reviews should identify opportunities for Continuous improvements by reducing process variability, narrowing down Process control parameters and ranges to achieve more consistent CQA performance; this will take the companies toward 6-sigma quality.
Written procedures are not drafted, reviewed and approved by appropriate organizational units and reviewed and approved by the Quality Control Unit.
Leave a Comment
You must be logged in to post a comment.