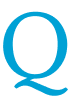
USFDA Warning letter to Mylan in 2020 cited inadequate procedures to monitor and control recovered solvents, impurity risks associated with solvents, unknown peaks in recovered solvents. The Warning letter to Mylan Laboratories Unit 7 Pashamylaram, India (FEI 3003227156) followed inspection of the unit from 24-28 February 2020.
Failure to implement procedures to evaluate and control impurity risks associated with solvents, recovered solvents, inadequate testing, establishing impurity profile and standards and maintain a program for monitoring process control to prevent unanticipated impurities in API manufacturing operations. Only the main peak is evaluated during analysis by the Firm and failed to evaluate the unknown peaks observed during analytical testing of solvents. Unknown peaks observed in chromatograms may represent unanticipated impurities and should be thoroughly evaluated, and if necessary, investigated.
Firms response to agency the recovered solvents utilized at this facility had minimal impact on API and API intermediates based upon the absence of out-of-specification investigations, lack of complaints, and undetected impurity testing is inadequate. Evaluation of the unknown peaks observed in recovered solvent chromatograms was not comprehensive and did not include a thorough manufacturing evaluation to determine if solvent recovery process contributed impurities to the recovered solvent.
In response to the Warning letter, Firm to provide:
Failure to implement procedures to evaluate and control impurity risks associated with solvents, recovered solvents, inadequate testing, establishing impurity profile and standards and maintain a program for monitoring process control to prevent unanticipated impurities in API manufacturing operations. Only the main peak is evaluated during analysis by the Firm and failed to evaluate the unknown peaks observed during analytical testing of solvents. Unknown peaks observed in chromatograms may represent unanticipated impurities and should be thoroughly evaluated, and if necessary, investigated.
Firms response to agency the recovered solvents utilized at this facility had minimal impact on API and API intermediates based upon the absence of out-of-specification investigations, lack of complaints, and undetected impurity testing is inadequate. Evaluation of the unknown peaks observed in recovered solvent chromatograms was not comprehensive and did not include a thorough manufacturing evaluation to determine if solvent recovery process contributed impurities to the recovered solvent.
In response to the Warning letter, Firm to provide:
Companies should have procedure for qualification of recovered solvents for use in processes considering all possible carry over impurities (reagents, degradants, stabilisers, impurities etc.). It is not sufficient to have specifications for recovered solvents with only chromatography purity for main component. Map all possible carry over impurities (reagents, solvents, degradants, impurities) into recovered solvent. Consider that all components in the process matrix are potential carry over impurities into recovered solvent. Establish detailed specifications for recovered solvent including limits for other solvents and reagents with appropriately justified limits. Formally document the rationale for the defined specification for each recovered solvent.
QA/QC teams should be made aware of /appropriately trained to report abnormal observation of unknown peaks in recovered solvents. Assumption that since a solvent is recovered from same process and used back carry over impurities do not matter & since recovery involve distillation, non volatile impurities will not be present in recovered solvents.
Monitoring and control of unknown impurities from fresh solvents is also important. Firms should know through a process of Qualification of solvents and sources and information collected from vendors, transporters what are possible impurities in the fresh solvents(e.g., stabilizers/additives, contaminants from transport due to previous solvents transported etc.) which may pose a risk for carry over into the API.
Establish procedures for Qualification of fresh solvents (sources, vendors), and defining appropriate specifications for fresh solvents (which cover possible impurities and consttituents in the solvent such as stabilisers / additives). Collect adequate information on solvents from the vendors, from literature to establish the controls. Establish procedure for evaluating any contamination due to transport (due to previous material carried by bulk solvent carriers/tankers) – cleaning certificates and previous material declarations from transporter, evaluation of cleaning procedures used by transporter, periodic audits, transport agreements.
Leave a Comment
You must be logged in to post a comment.