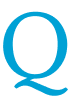
Warning letters, 483s, Recalls, Import Alerts, Audit observations
Accord healthcare recalled from US market Daptomycin for Injection 500 mg/vial and Daptomycin for Injection 350 mg/vial for labelling mixup. Recall followed a complaint that vials labelled as Daptomycin for Injection 500 mg/vial were found in cartons labeled as “Daptomycin for Injection 350 mg/vial. The product were manufactured by Intas Pharmaceuticals, India.
Accord Healthcare, Inc. is voluntarily recalling a single lot of Daptomycin for Injection 500 mg/vial, and Daptomycin for Injection 350 mg/vial product contained in cartons imprinted with lot # R2200232 Exp: 01/2025 to the consumer/user level.
Accord received a product complaint report from a hospital pharmacy that vials labeled as “Daptomycin for Injection 500 mg/vial” were found in cartons labeled as “Daptomycin for Injection 350 mg/vial”. The lot and expiration date printed on the outer carton and inner vial are the same and correspond to “Daptomycin for Injection 500 mg/vial.” Accordingly, Accord is voluntarily recalling all of lot #R2200232, Daptomycin for Injection 500 mg/vial, which may be in outer cartons that read “Daptomycin for Injection 500 mg/vial” OR “Daptomycin for Injection 350 mg/vial.”
The lot number, NDC number and expiration date of affected Daptomycin 500 mg/vial and Daptomycin 350 mg/vial product is shown in the table below:
Product | NDC | Lot number/Expiration Date |
Daptomycin for Injection 500 mg/vial | 16729-435-05 | R2200232, 01/2025 |
Daptomycin for Injection 350 mg/vial | 16729-434-05 |
It is typical to have reduced change over cleaning and line clearance requirements when different strengths of a product manufactured / packed in same line. Companies should evaluate, perform risk assessment and implement systems, procedures to prevent product mixups, with adequate line clearance procedures for change over, adequate batch /lot segregation, in process labelling, control on dispensing, issuance, handling of printed packing materials – labels, cartons, outer cartons.
Leave a Comment
You must be logged in to post a comment.